At Wiggers, we make it as easy as possible for our customers. By thinking in solutions, we simplify and accelerate production processes in the construction, finishing and interior design industries.
With a combination of high-quality products and a streamlined process, we continuously realise our customers' goals and ambitions. By continuously innovating and thinking ahead, we make every project for our customer more cost-effective and sustainable, with minimal waste of materials, time or effort.
"Thanks to our complete control of production processes and the craftsmanship of our employees, we dare to take on any challenge."
Gerrit Hartman
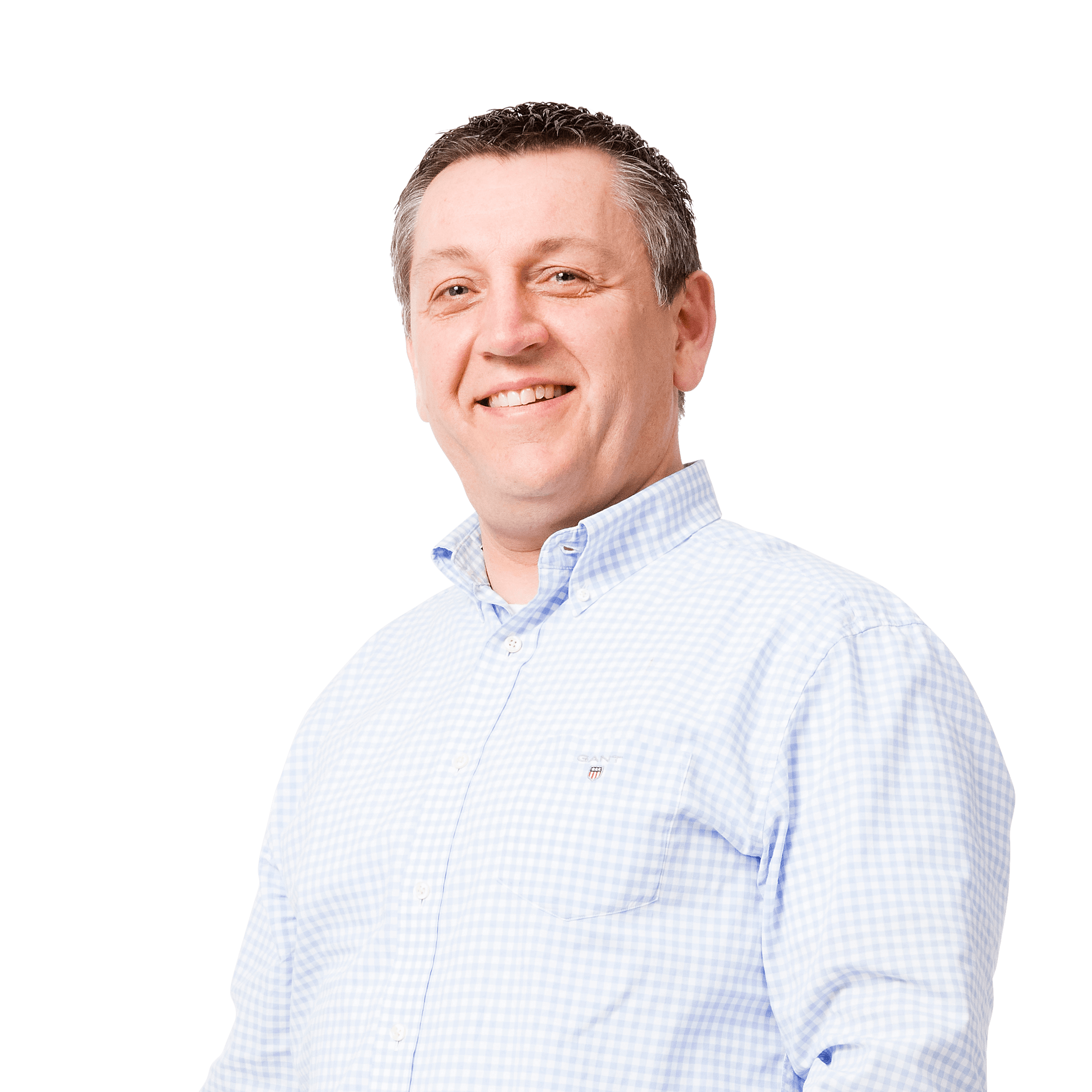
EcoProfiel
Sustainable casing profiles for the construction industry
EcoProfiel is a range of products fully focused on construction. Complete, yet flexible and customer-specific. The profiles are ready-to-use, sustainable products for construction. Examples include reveal trim, pipe ducts, skirting boards and windowsills.
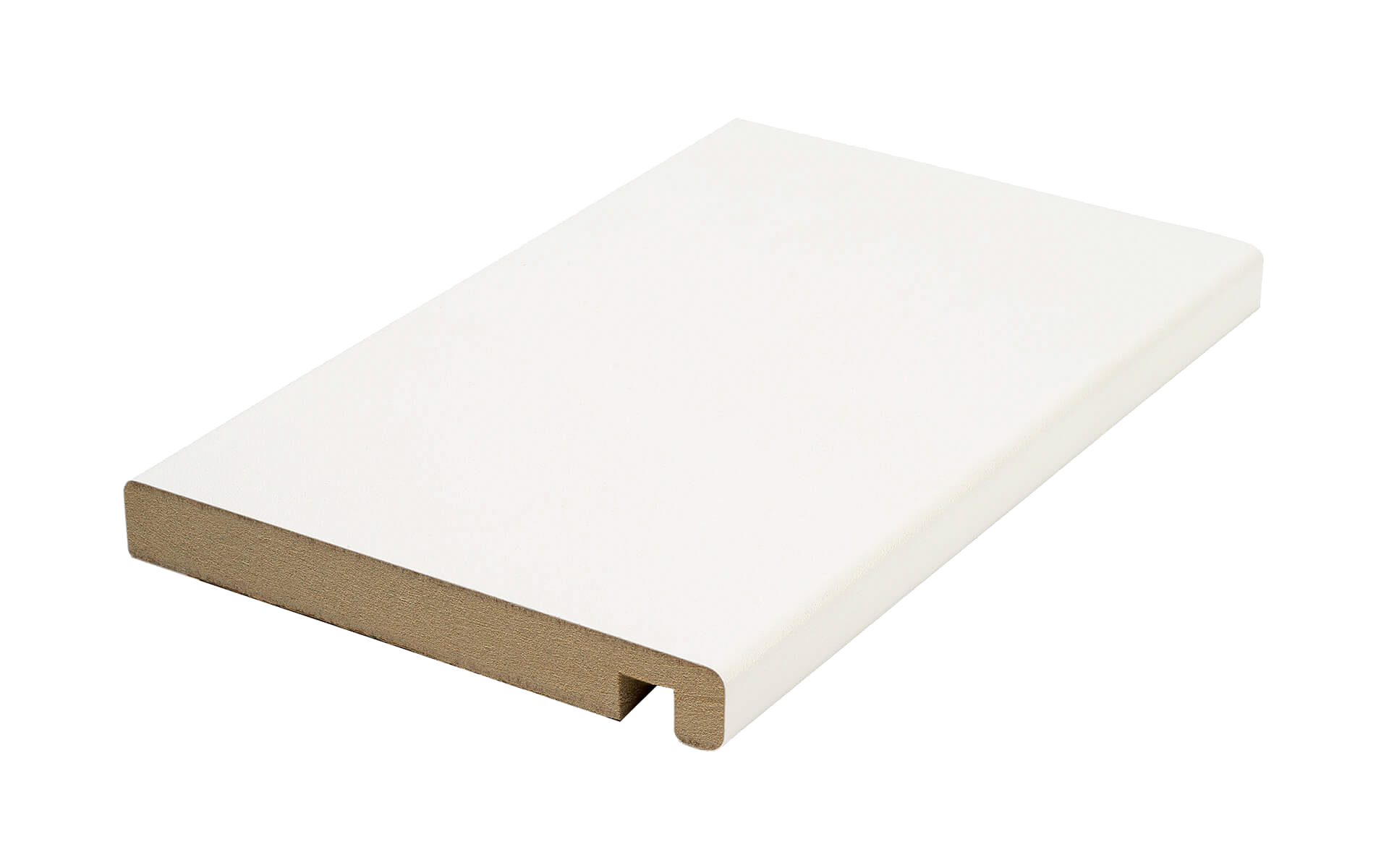
The power of Wiggers
Thanks an excellent collaboration with our customers, we know and understand your challenges. This enables us to deliver solutions that perfectly match your needs and projects. Always ready for installation. Because we have moved the work from the construction site to our factory. This saves production steps, manpower and waste on location.