Our own building as the ultimate frontpiece
We develop and produce beautiful solutions for the construction, finishing, interior design and industry sectors on a daily basis. We are always happy to share the end results! This time, the focus is on us: this is how we tackled the finishing of our building in Winterswijk. Because our own work environment is of course also full of our own products and solutions.
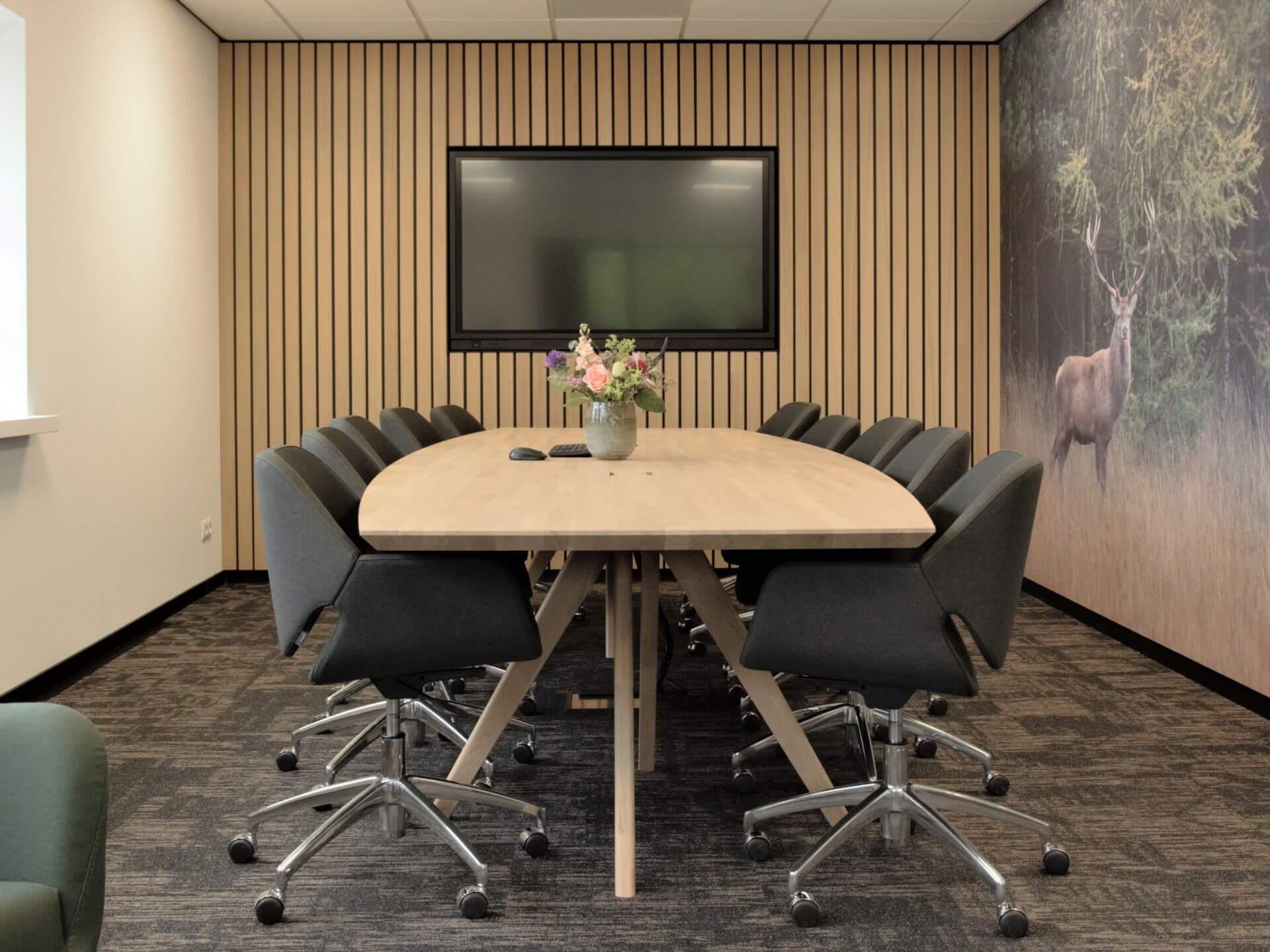
Self-produced and assembled
During the design phase, we consciously opted for one clear style together with the architect, with European Oak veneer as a connecting element. This line has been consistently applied in the office area of our building: the reception hall, conference rooms, open-plan office and even the kitchen. Wall coverings, reveals, long windowsills, glazing beads and various custom solutions are found everywhere. "Everything we can make ourselves, we made ourselves," says Han Siemerink, account manager. "And it was all assembled by our own co-creators. Because our products are ready to assemble, they were able to install everything on site quickly and efficiently. Exactly how we approach our customers' projects."
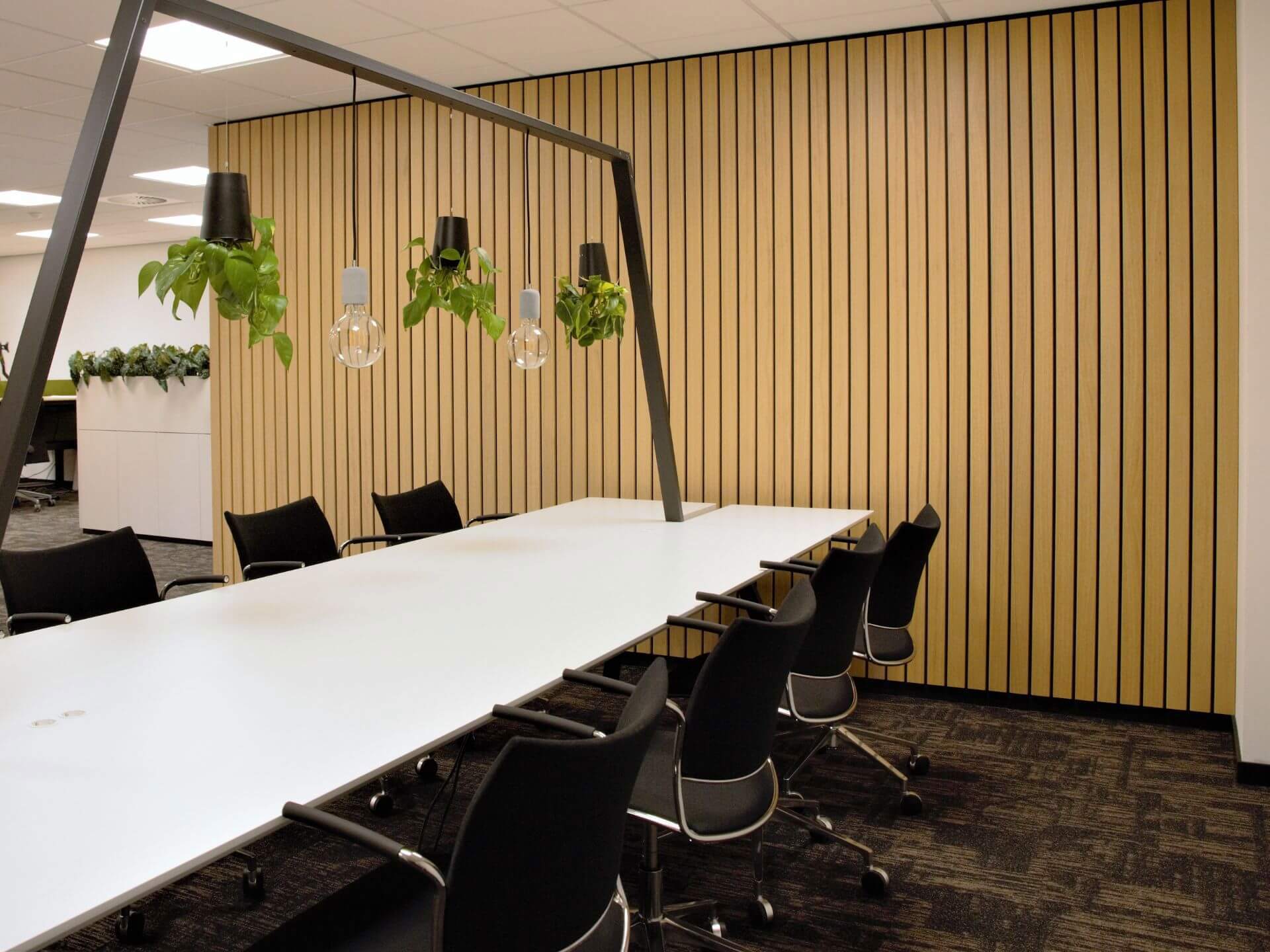
A work environment to be proud of
The European Oak veneer line has been continued in the areas surrounding the factory. The staff entrance, production office and canteen are just as carefully designed as the office area. Our wall panels, frame finishing, windowsills and radiator screens have also been used in these spaces. "We now also enjoy our own work during our lunch break," says Han. "The result is a work environment in which our products are not only visible, but also tangible. A great example of how appearance and functionality come together in our total solutions."
The power of Wiggers
Thanks an excellent collaboration with our customers, we know and understand your challenges. This enables us to deliver solutions that perfectly match your needs and projects. Always ready for installation. Because we have moved the work from the construction site to our factory. This saves production steps, manpower and waste on location.